The Perfect Match: Digging Deep to Restore the Wyoming State Capitol
An earlier version of this article originally appeared in the Fall 2022 edition of Building Stone Magazine.
Just one highway leads to Rawlins, Wyoming, a small city 150 miles northwest of the state capital of Cheyenne. Rawlins straddles interstate route 80, but otherwise has drawn little attention to itself since its glory days in the 1800s, when it served as a freight and passenger stop on the Transcontinental Railroad.
In the late nineteenth century, a quarry here produced sandstone for construction projects throughout the region. Rawlins sandstone glows in sunlight with a warm gray that lends a stately air to building exteriors, making it particularly attractive to designers of ornate government edifices. Overseeing the quarry’s production, owner Hans Larsen knew that this high-quality stone should be the fundamental material to grace the Wyoming territorial capitol building, for which construction began in the mid-1880s, several years before Wyoming received statehood. However, the architects had specified sandstone from Loveland, Colorado for the foundation and the capitol steps, with plans to bring more of this stone from Loveland to create the ornamented façade.
Hearing of this insult to Wyoming quarries, Larsen stormed into Cheyenne, demanding that the local government use materials from its own resources rather than importing stone from another territory’s quarry. Government officials, no doubt taken aback by this fiery businessman, saw the wisdom in his point. Larsen won the contract, making Rawlins sandstone the material of choice for the capitol’s impressive exterior. Skilled stone masons created hundreds of detailed sculpted features by hand. Each column, corner, and cornice was a unique tribute to the sandstone’s quality and durability. The finished structure, including the towering rotunda, opened in 1888.
Not even Wyoming sandstone can last forever, however, so some 130 years later, Wyoming’s infamously harsh winters had taken their toll on the original building, as well as the additions to Capitol Square constructed in 1890 and 1917. In 2013, the state began a massive $299 million renovation of the entire capitol complex, bringing top talent from across the region to Cheyenne to restore the grandeur of this splendid Renaissance Revival façade. The state determined that the restored capitol should look exactly as it did when the first crew completed it in 1888, so the team of architects, masons, and fabricators looked northwest to Rawlins once again for stone to match the building’s worn exterior.
But Rawlins no longer had a working stone quarry. The quarry had closed in the 1920s, nearly 100 years before.
Unearthing the Stone
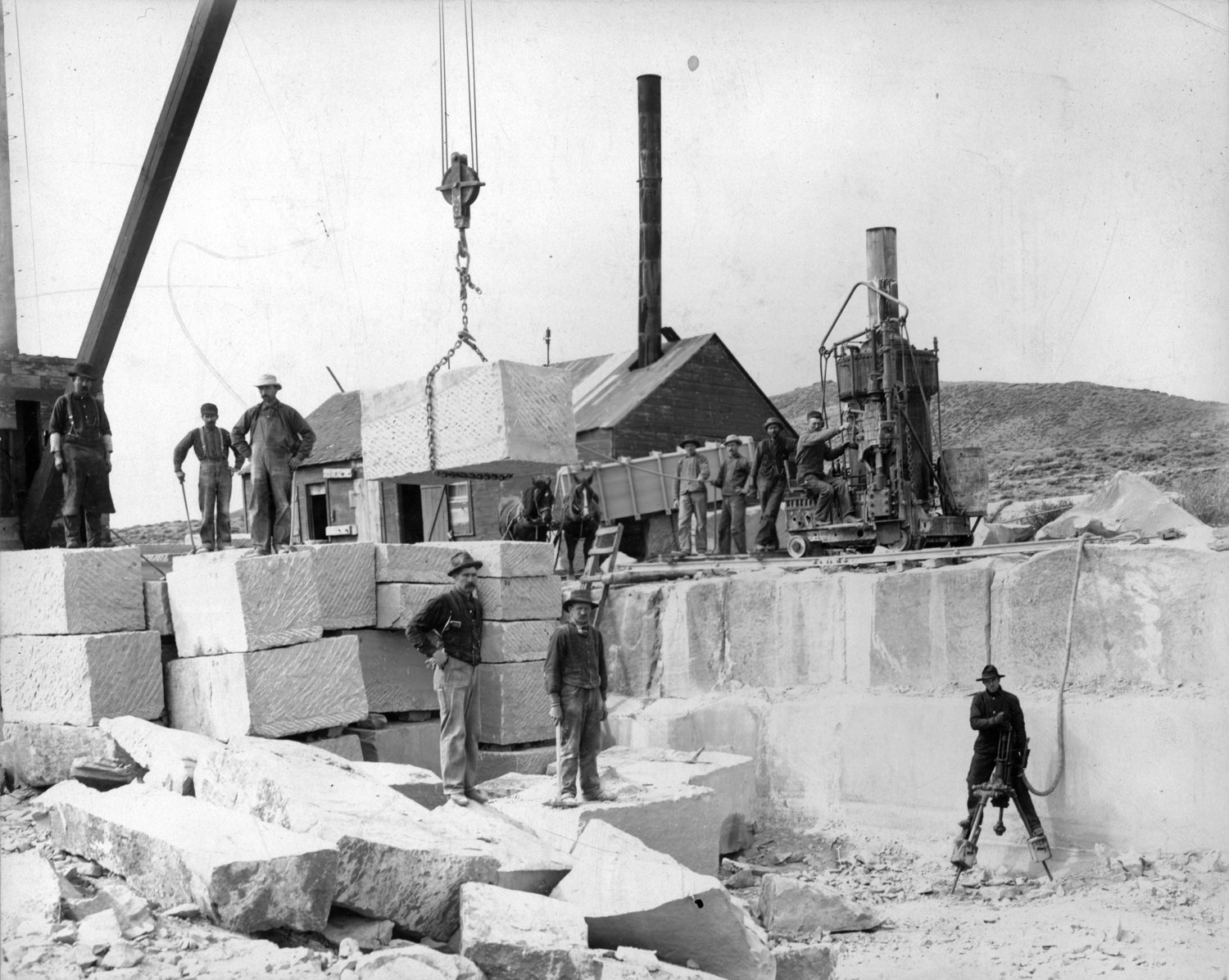
A block of sandstone is hoisted by a stiff leg derrick in a sandstone quarry owned by the Kerr Marle and Stone Company near Rawlins, WY between 1890 and 1910. It is believed that this photo might be the same quarry used in the Wyoming State Capitol restoration. Photo courtesy Wyoming State Archives.
The land containing the former quarry now belonged to Overland Trail Cattle Company, a major ranching and cattle operation and a subsidiary of Anschutz Corp, a private equity company based in Denver, Colorado.
“Eldon Strid, a local person, provided a tremendous amount of knowledge about where the quarry was and who the owners were,” said Jeff Callinan of J.E. Dunn Construction Company, the general contractor for the state capitol project. “The land had recently changed hands—they were about to put a wind farm on this land.”
J.E. Dunn tried to contact the owners, but when they received no response, they enlisted the help of the governor’s office of the State of Wyoming. Governor Matt Mead and his staff approached Anschutz and “managed to shake it loose,” Callinan said, striking a deal that allowed the state to take 253 tons of sandstone from the former quarry for a reasonable price, providing the state found its own people to bring out the stone. J.E. Dunn tackled this tall order and located a mobile quarry operator in South Dakota.
“We’d never had to set up a mobile quarry before,” said Callinan. “Normally, we are in the business of going out to the quarry to select big blocks of stone. In this case, we had to learn about the front end and getting the stone extracted. It’s a logistical project to get the stone out of the earth and get it to the people who can create a piece to go into the building. This team knows how to go through that logistical challenge.”
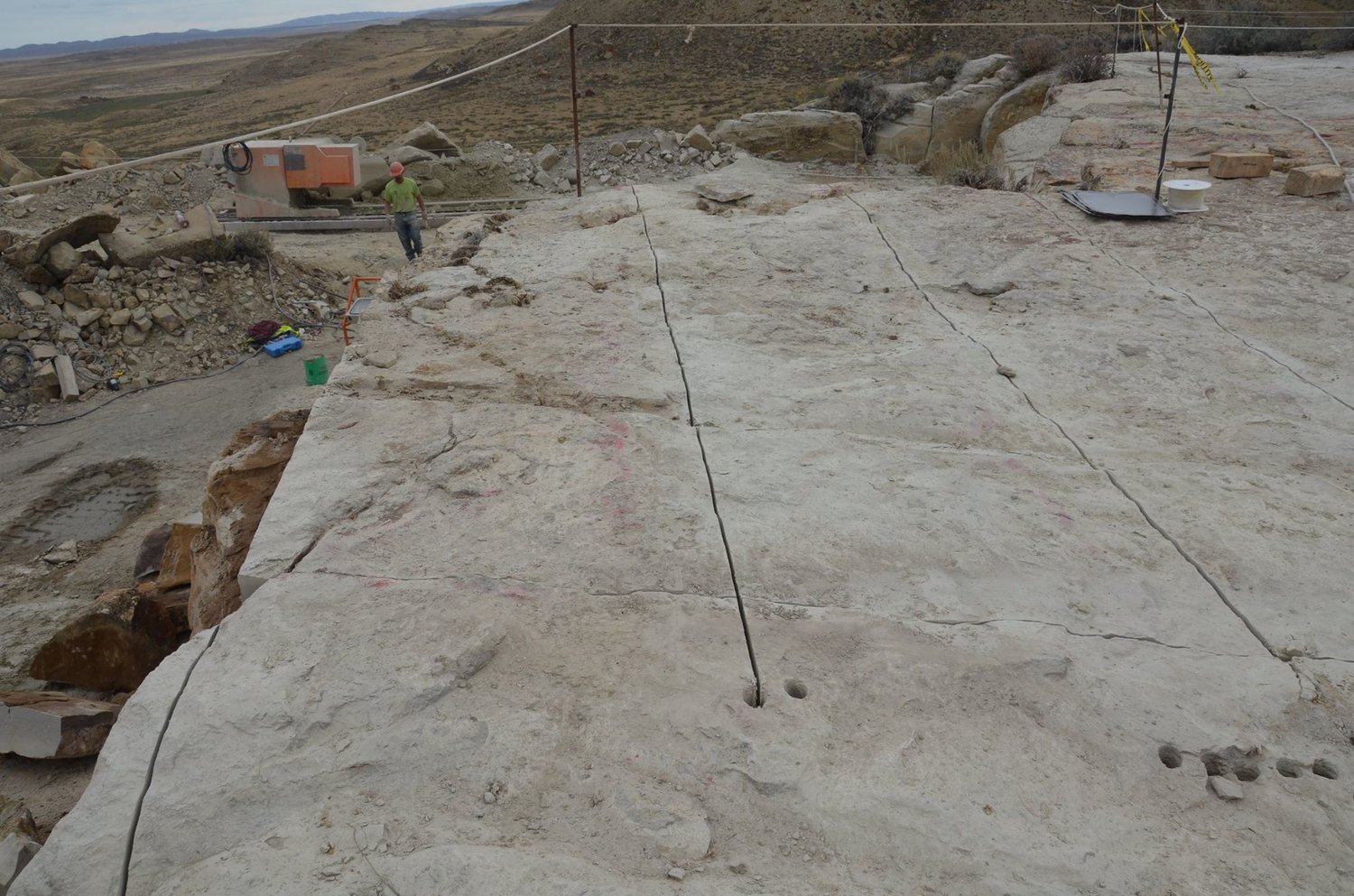
The governor’s office of the State of Wyoming helped in the access in the capitol’s former quarry source in Rawlins, WY, which had closed nearly 100 years before. 235 tons of sandstone were quarried and used in the restoration effort. Here, cuts are made in the sandstone where sections of block will be extracted using a wire saw. Photo courtesy State of Wyoming.
Setting up a mobile quarry came with its own package of obstacles, Callinan explained. “We had to build a road. We had to coordinate with the Department of Corrections because there was a prison nearby. Then the Fish and Wildlife Department identified that a golden eagle was nesting in the area.” Golden eagles are a protected species under the Bald and Golden Eagles Act of 1940, so the quarry team had to wait for a month to begin their work until the eaglets had fledged and the birds abandoned the nest.
The effort to reopen the long-dormant quarry proved to be more than worthwhile, said Tom Van Etten, president of Galloy & Van Etten, Inc., an award-winning family-owned stone fabrication company in Chicago. Van Etten led the twelve-person team that turned the Rawlins sandstone into meticulously cut and sculpted replacement pieces for the Wyoming project. “It’s a perfect match,” he said. “They found not just the right quarry, but the right stone matching in color.”
Choosing exactly the right cuts of sandstone—matching the color of each to the existing stonework in the capitol façade—became the full-time job of preservation architect Katie Butler of CSHQA, headquartered in Boise, ID. Butler and CSHQA principal John Maulin came into the state capitol project in 2015 at the request of HDR Architecture, Inc., the architect of record. “I visited the site in Wyoming almost every other week for three years and attended numerous trips to quarries and fabricators to select the stone, review samples, and ensure the processes were in compliance with the construction documents,” said Butler.
The process began with the team comparing a series of seven Rawlins sandstone samples, ranging in color from gray to buff, to each building level and elevation of the three building periods. “After a day on a lift, three samples were consistently found to match the existing stone at all areas,” said Butler. “These three samples established the range of colors we would use to select blocks from the Rawlins quarry.” The team visited the quarry three times between October and November 2015 to determine if the 3’ x 3’ blocks were in the correct range for color and veining.
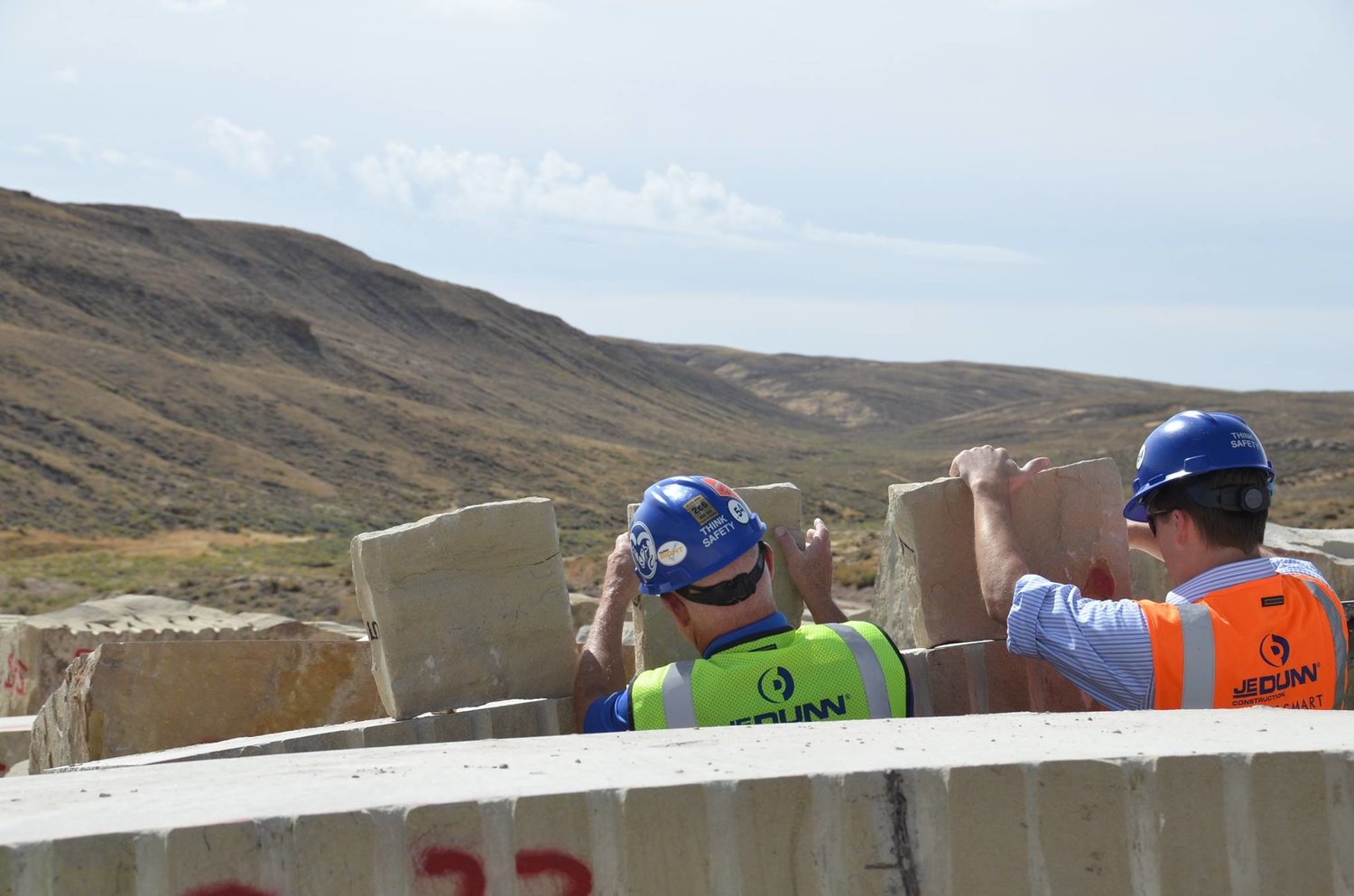
The project team compares samples to quarry blocks. Tom Van Etten, president of Galloy & Van Etten, led the twelve-person team that turned the Rawlins sandstone into meticulously cut and sculpted pieces for the Wyoming project. Photo courtesy State of Wyoming.
“It was quite the process,” said Butler. “At each site visit, we reviewed stone from different parts of the quarry—south pit, middle pit, and north pit. It was all the same type of sandstone but varied from each part of the quarry. It was tough trying to make sure that the underlying color and variation would be appropriate, especially with the building having been built in multiple phases.” After each visit, the team documented the process with photos and summarized it all in a field report.
When stone became available from the Colorado quarry in Loveland for repairs of the stairs on the north and west side of the building, Butler and her team repeated this painstaking comparison until they found the right match for the existing steps.
With this process completed, Butler and the rest of the team—Scott Evett from masonry contractor Mark 1 Restoration Company; Mike Ford, senior associate with stone restoration architect Wiss, Janney, Elstner Associates, Inc. (WJE); and representatives from J.E. Dunn, HDR, and the State of Wyoming met on site regularly to review mockups, trial repairs, and overall project progress.
Enormous Scope
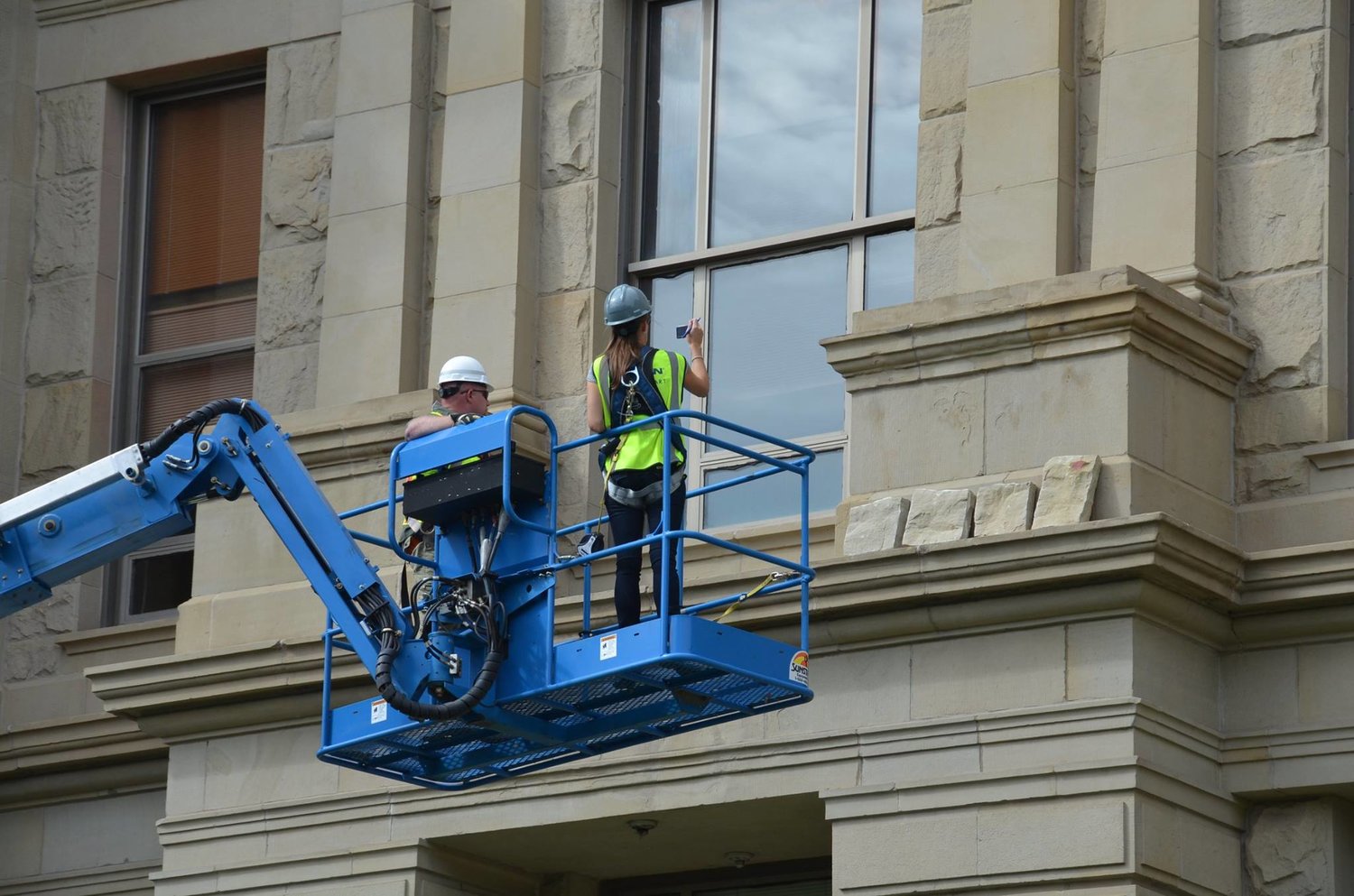
The process began with the team comparing a series of seven Rawlins sandstone samples, ranging in color from gray to buff, to each building level and elevation of the three building periods. “After a day on a lift, three samples were consistently found to match the existing stones at all areas,” said Butler. Photo courtesy State of Wyoming.
While the historians searched for exactly the right stone, Ford and the WJE team worked with Mark 1 Restoration to determine the scope of the required repairs. “It was about developing a repair approach that we thought was good and sound, but prioritized enough that we could do the repairs we felt were most important, deferring others,” said Ford. “We went on site, did an investigation, and provided options for repair.”
Placing life safety above all other priorities, the WJE team discovered that the stone at the base of the building—the two courses quarried in Loveland—had deteriorated enough to raise concerns about its continued viability. A clear surface treatment had been applied to this stone in the 1990s, but it did not prevent damage from water and weather, and it “likely accelerated deterioration,” a report on the project noted. Many of the cornices and column capitals showed “severe delamination,” the document continued, also due primarily to water exposure. Some areas had been patched with mortar and stabilized with protective netting, applied years before to slow the progression of the inevitable—and to keep pieces of the façade from raining down on passersby.
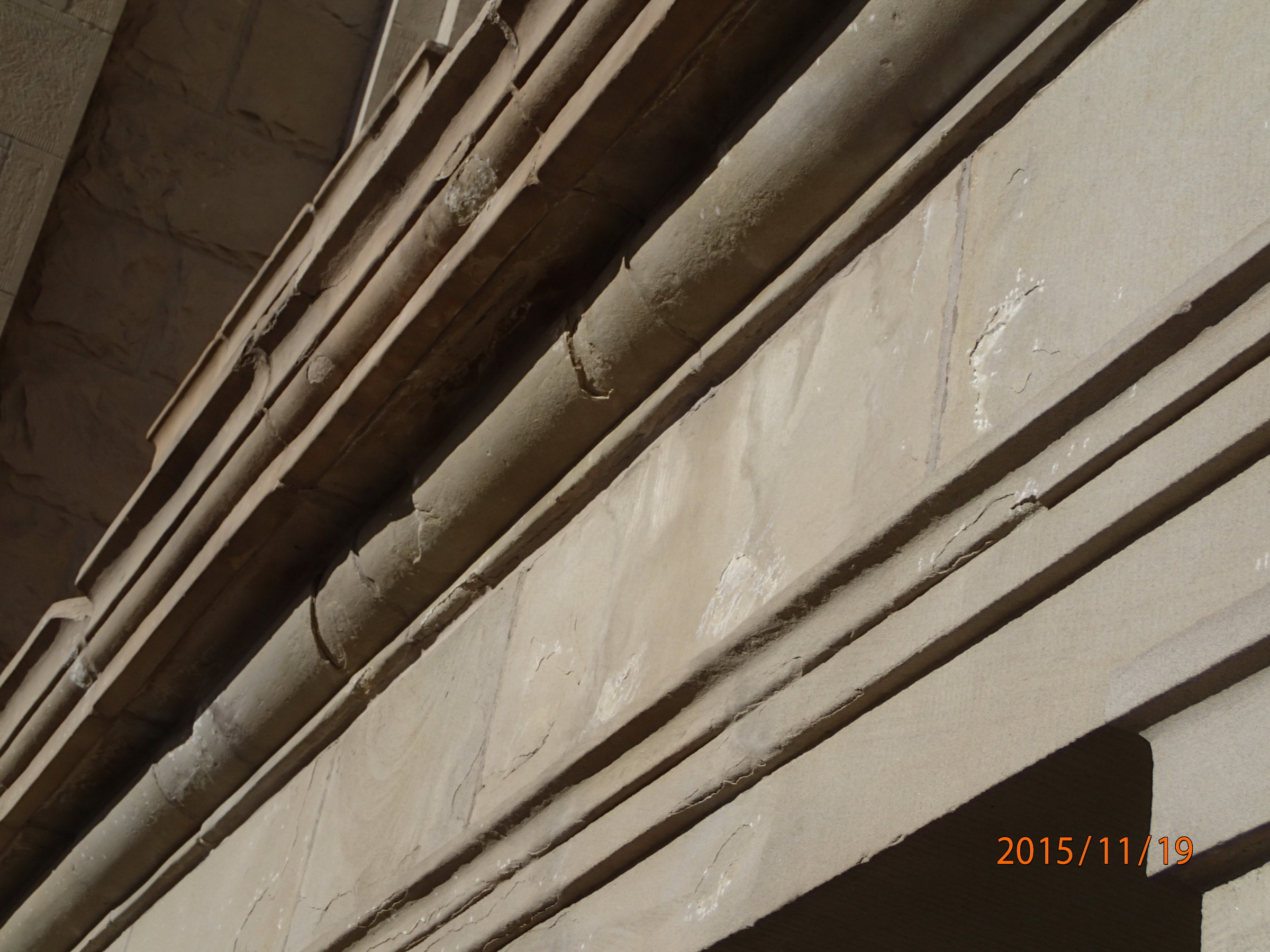
The ornate elements throughout the Capitol façade had deteriorated during more than a century of Wyoming weather. Photo courtesy Wiss, Janney, Elstner Associates, Inc.
When it came to the restoration of these decorative elements, Ford and his team presented the state with options. “Often people look at these projects and say, ‘I can’t do that,’ instead of ‘Yes, I can do it, and this is what it will look like,’” he said. “For example, if you have snow and it sits on cornices and ledges and it melts, it gets into the stone and it absorbs. Then it freezes, and it happens again and again—that’s called thermal cycling, or freeze/thaw. A lot of the distress we were seeing was at these projecting ledges. We said that we could do dutchman repairs to match the original, and could improve water management; however, another approach could include installation of a sheet metal flashing. This may address water management and be more cost effective, but it would have an aesthetic impact.”
WJE installed a mockup of both the stone dutchman and flashing approach and showed the state. The state chose the dutchman approach. “That is fine; they were able to make a good decision with the mockups and an understanding of the benefits and drawbacks we presented,” said Ford. “It’s a historic building. You want to keep the historic character and integrity.”
In all, a total of 1,135 individual pieces throughout the building’s exterior required repairs or replacement, using 3,160 cubic feet of stone. “We put the stone in a local yard until we shipped it to Galloy & Van Etten in Chicago,” said Callinan. “There were truckloads and truckloads and truckloads.”
As if the size and scope of the project were not complex enough, the original architect in the 1880s, Davis W. Gibbs, had designed just about every feature of the ornate European-inspired façade to be unique.
- Installation of the fabricated replacement piece was only the beginning of each repair. Detailed work by hand reshaped and restored the Capitol’s original grandeur.
- Photos courtesy Wiss, Janney, Elstner Associates, Inc.
“As a masonry restoration fabricator, Mark 1 created a shop drawing for each additional piece,” said Callinan. This shop ticket included the type of stone, its dimensions, the dutchman repair styles required, the number of the actual block of stone from which this piece would be cut, elevation drawings, and tooling requirements. “These would be approved, and it would go into fabrication. A lot of times they oversize them a little bit, so onsite they can tool it a little bit to get a perfect fit. Some have similar profiles and textures, but each piece was fabricated for a specific place and purpose.”
The masonry team worked to develop standardized details for categories of stone profiles—so all the cornice ledges, for example, had the same basic shape and required the same kinds of onsite work once they arrived at the job site. “Every stone on the building was assigned a number, so you could see all of these on the elevations,” said Butler. Tom and Susan Van Etten led the effort at their Chicago facility to fabricate the profile of each element, roughing in the shape and preparing it for the decorative carving to be done by hand in Cheyenne.
- Many levels of scaffolding allowed stone masons and architects to compare the newly quarried Rawlins sandstone to the building’s higher levels. Photo courtesy Wiss, Janney, Elstner Associates, Inc.
- Galloy & Van Etten turned the raw sandstone into precise shapes for finishing at the job site. Photo courtesy Galloy & Van Etten.
On site, masons from Mark 1 installed the dutchmen that had been fabricated in Chicago at Galloy & Van Etten with planers, pneumatic chisels, combing tools and other shaping devices to create exact replicas of the original detail for each column and cornice. Portions of the building were hand-finished on site—the rock face of the base stone, for example, using a small pitching tool to remove bits of material at a time.
Butler totaled up the various kinds of repairs the project required: four different kinds of joints, eight different resurfacing techniques, 33 kinds of dutchmen, and two types of surface treatments. “WJE and CSHQA worked as a team,” she said. “WJE reviewed each repair for structural integrity and watertightness, while CSHQA would take the lead on the aesthetic appearance. There were only a couple of occasions where we had to change something because the stone wasn’t a good match.”
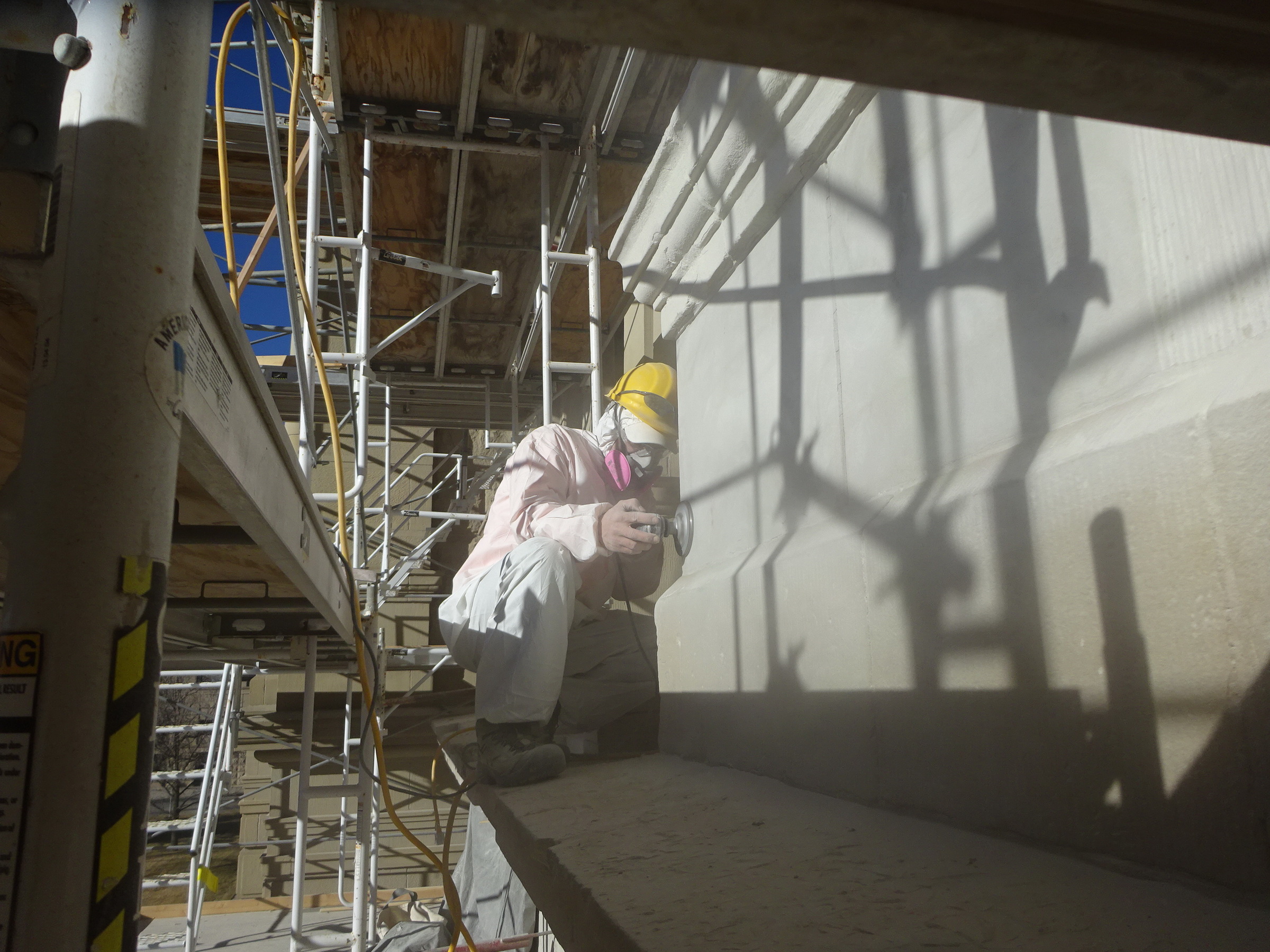
Every facet of the stone restoration required meticulous work by hand using small tools. Photo courtesy Wiss, Janney, Elstner Associates, Inc.
The Reopening
Four years of overhaul—the complex’s first major renovation since 1917—resulted in a state capitol worthy of the accolades it has received. The stonework received the 2021 Grande Pinnacle Award from the Natural Stone Institute, while awards for the total project streamed in from many trade organizations: the American Public Works Association, Building Design and Construction magazine, the American Council of Engineering Companies of Colorado, the Construction Management Association of America, and Engineering-News Record Mountain States.
“A project like this takes extraordinary skill, but it takes a team that knows who the right players are to accomplish it,” said Callinan. “It was extremely helpful to bring the right artisans to the table. The stone masons who were carving the stone onsite were the same people who worked with us on two other state capitol projects.”
State capitol restoration stands in a class of its own, said Butler, making this her favorite kind of work. “There are only fifty state capitols,” she pointed out, “so it’s a really special building type. It’s fun to see how things can be put back together and preserved without it looking like it was ever touched.”