Manufacturing Impacts: Natural Stone vs. Terrazzo
Terrazzo has a long history, informed in part by the ancient mosaics of Egypt that were made of small or irregular pieces of stone, glass, or ceramic. Today, terrazzo is a composite building material that is poured in place or precast. It is typically used for flooring, wall treatments, and decorative items. Terrazzo often contains chips of marble, quartz, granite, glass, or aggregates such as metal. In the 1970s improvements were made to the manufacturing process that helped terrazzo become a popular building material suitable for large applications. These improvements made the material stronger and more lightweight. They also created a wider selection of colors and installation thicknesses.
- Terrazzo Sample #1
- Terrazzo Sample #2
Terrazzo is a durable, low maintenance material. It is nonporous and can be slip resistant. Some terrazzo is very slippery and can be a hazard when wet. Because of the wide range of materials used to make terrazzo there is a lot of design flexibility. Shapes and medallions can be fabricated onsite by using metal or glass divider strips which were created to prevent the cracking that was typical with earlier uses of the material.
Terrazzo is positioned as a sustainable material because it often contains recycled content and is made with little-to-no volatile organic compound (VOC) materials. It does not off-gas or produce irritants. There are several types of terrazzo, but most of the terrazzo installed today is epoxy-based. A disadvantage of epoxy-based terrazzo is that it can only be used for interior applications. This type of terrazzo will lose its color and peel when used outdoors. Cracking is
the most common form of failure. However, the cracking is usually not caused by the terrazzo itself. Instead, it is caused by the structural support system, which may be wood or concrete. Contact with alkalis or acids can cause deterioration of the bonding agents used in the terrazzo. The multi-step and energy intensive processes involved in manufacturing terrazzo result in a much larger environmental footprint than natural stone.
Manufacturing Natural Stone vs. Terrazzo
Several raw materials are required to manufacture terrazzo, including limestone, marble, glass, or quartz. These materials are mined or quarried out of the ground and then transported to a manufacturer or plant to be sorted. The cement or resin binders and additives such as pigments, sealers, and fibers also need to be manufactured. The products are all mixed with the aggregates and additives are incorporated. The mixture is poured onto a surface such as concrete or into a mold. Then the material must dry and cure before it is grinded with a terrazzo grinder. If there are depressions left by the grinding process, they are filled with a matching material for a smooth, uniform surface. The final product is then cleaned, polished, and sealed.
In contrast, natural stone requires only quarrying, fabricating, finishing, and transporting. No additional materials or chemicals are required to create natural stone. The Earth naturally forms the material over time. This means natural stone really is a natural material and has many other attributes, including its durability, recyclability, and wide range of aesthetics. Natural stone can be used in many different types of indoor and outdoor applications. It is a healthy material and contains no VOCs, which means it does not emit any harmful gases.
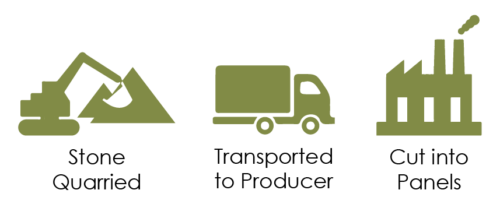
Manufacturing impacts of natural stone.
Natural stone can be used for both interior and exterior projects to create unique patterns that feature the natural variations in color, veining, and texture of the material.
Sustainability Concerns
From an overall sustainability perspective, natural stone has a lower environmental footprint than terrazzo. This is due to the minimal resources used to quarry, fabricate, finish, and transport natural stone. As the table and chart below demonstrate, the manufacturing of terrazzo has a higher global warming potential (GWP), ozone layer depletion, and smog formation than natural stone. Each step in the terrazzo manufacturing process requires the use of energy, which contributes to the total GWP. The larger the GWP, the more that a given gas warms the Earth compared to carbon dioxide (CO2) over the same timeframe. The natural stone industry is sometimes criticized for utilizing raw materials that are not rapidly renewable. However, natural stone is abundant within the Earth. Other industries also utilize the supply of natural stone as it is a significant ingredient in terrazzo, concrete, porcelain, and other manmade products.
The impacts of these processes have been documented and systematically compared against other materials using the same environmental criteria. This information is a valuable resource when selecting a sustainable material for a project.
Sample environmental impacts for a terrazzo product versus a granite from Environmental Product Declarations (EPDs).
These characteristics and attributes also make natural stone a great choice when seeking a green building rating certification within the U.S. Green Building Council’s Leadership in Energy and Environmental Design (LEED) or the International Living Future Institute’s Living Building Challenge (LBC). The different manufacturing processes and impacts of building materials are being documented in product labels such as Environmental Product Declarations (EPDs) and Health Product Declarations (HPDs). These labels make it even easier to qualify for points and credits within LEED and other green building rating systems using natural stone. The labels document and quantify environmental information on the life cycle of a product and allow you to make comparisons and informed decisions on materials that fulfill the same function. The product labels are also intended to demonstrate that the health and environmental claims are transparent, accurate, and meet defined standards. Industry-wide EPDs are available for natural stone cladding, flooring/paving, and countertops. HPDs are available for common natural stone types used in the dimension stone industry including granite, limestone, marble, quartzite, onyx, sandstone, slate, travertine, and more. (See also: Environmental and Health Product Labels for Natural Stone.)
To further advance these issues, the natural stone industry has been working diligently to make continuous improvements in each area and step of the process. This includes reducing water use, energy use, improving the efficiency of the transportation of natural stone, and properly managing and adaptively reusing quarry sites.
Technology advancements in the natural stone industry help reduce the use of energy and water and create strategies that use every part of a stone block. Photo Credit: Stephanie Vierra
The natural stone industry also created a certification system that determines if a quarry or fabricator meets defined sustainability standards in key areas of importance. This makes it easier to find and use natural stones that meet the standard, simplifying the process of choosing the right material that not only looks and performs well, but also has the least amount of impact on the environment. The standard is also accepted within the LBC, further ensuring its use in sustainable building projects. The metrics of the Natural Stone Sustainability Standard can be used to vet stone suppliers even if they have not yet achieved certification. More information is available via the Natural Stone Institute or NSF International.