Manufacturing Impacts: Natural Stone vs. Porcelain
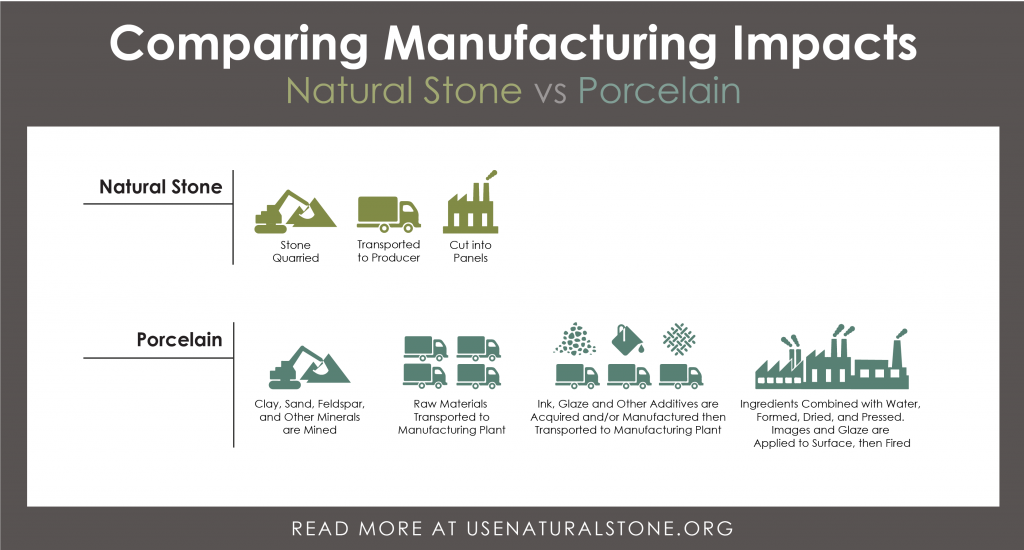
Porcelain is a hardwearing material that is suitable for both indoor and outdoor design projects. Porcelain slabs or tile are often used for kitchen and bathroom counters, flooring, stairs, and windowsills. It is a fairly thin material, typically manufactured to be only ½” thick. The basic ingredients that go into the process of manufacturing porcelain are clays, sands, and different feldspar minerals. Because it contains some natural materials, porcelain is often marketed as a sustainable material. Porcelain is also produced to emulate the beauty and veining of marble. But as you will see from the manufacturing process outlined below, the use of many materials and additives and the energy intensive processes involved in its manufacturing create a larger environmental footprint for porcelain than natural stone.
- Porcelain is often printed to mimic the beauty and veining of genuine marble. Photo courtesy of Stephanie Vierra.
- Arabescato marble
Manufacturing Porcelain vs. Natural Stone
Raw materials like clay, feldspar, and other materials must first be mined out of the ground and then transported to a manufacturing plant. The next step in the process is the intake, storage, and sorting of the required raw materials. Additives such as inks and glazes must also be transported to the manufacturing plant, where they undergo further sorting, mixing, forming, drying, and pressing. Images and glazes are applied to the porcelain surface at this stage. Then, extreme heat is required to fire and glaze the materials into the final porcelain product.
In contrast, natural stone requires only quarrying, fabricating, finishing, and transporting. No additional materials or chemicals are required to create natural stone. The Earth naturally forms the material over time. This means natural stone really is a natural material and has many other attributes, including its durability, recyclability, and wide range of aesthetics. Natural stone can be used in many different indoor and outdoor applications as well and contains no Volatile Organic Compounds (VOCs), meaning it does not emit any harmful gases, making it a healthy material.
Sustainability Concerns
From an overall sustainability perspective, natural stone has a lower environmental footprint than porcelain due to the minimal resources used to quarry, fabricate, finish, and transport it. All of the steps in the manufacturing process of porcelain require the use of a lot of water and energy which contribute to the total GWP. The larger the GWP, the more that a given gas warms the Earth compared to CO2 over that same timeframe.
These characteristics and attributes also make natural stone a great choice when seeking a green building rating certification within the U.S. Green Building Council’s Leadership in Energy and Environmental Design (LEED) or the International Living Future Institute’s Living Building Challenge (LBC). The different manufacturing processes and impacts of building materials are being documented in product labels such as Environmental Product Declarations (EPDs) and Health Product Declarations (HPDs). These labels make it even easier to qualify for points and credits within LEED and other green building rating systems using natural stone. The labels document and quantify environmental information on the life cycle of a product and allow you to make comparisons and informed decisions on materials that fulfill the same function. The product labels are also intended to demonstrate that the health and environmental claims are transparent, accurate, and meet defined standards. Industry-wide EPDs are available for natural stone cladding, flooring/paving, and countertops. HPDs are available for common natural stone types used in the dimension stone industry including granite, limestone, marble, quartzite, onyx, sandstone, slate, travertine, and more. (See also: Environmental and Health Product Labels for Natural Stone.)
To further advance these issues, the natural stone industry has been working diligently over the years to make continuous improvements in each area and step of the production process. This includes reducing water use, energy use, improving the efficiency of the transportation of natural stone, properly managing and adaptively reusing quarry sites, and many others.
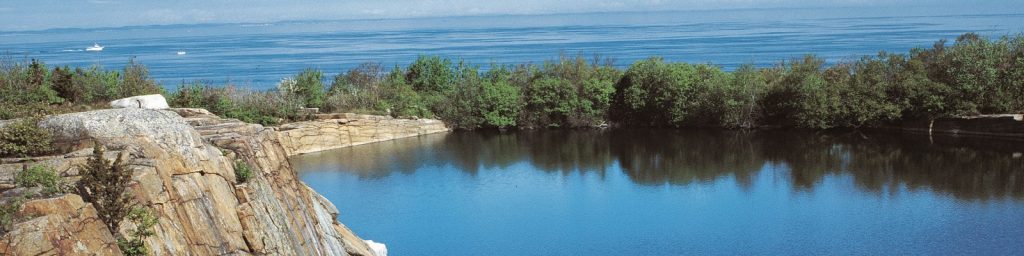
Halibut Point State Park in Massachusetts is a former granite quarry reclaimed into a public park. Photo courtesy of Mass.gov.
The natural stone industry has created a certification system that determines if a quarry or fabricator meets defined sustainability standards in key areas of importance. This makes it easier to find and use natural stones that meet the standard, simplifying the process of choosing the right material that not only looks and performs well, but also has the least amount of impact on the environment. The standard is also accepted within the LBC, further ensuring its use in sustainable building projects. Even if a natural stone is not yet certified to the standard, the information can be used to vet stone suppliers and ask important questions to help choose the optimal natural stone for your project. More information is available via the Natural Stone Institute or NSF International.